Rare earth elements (REEs) have emerged as essential building blocks for enabling the energy transition. This is particularly true for specific REEs needed to make REE magnets, which are used in e-motors and wind turbines.
With an expected surge in demand for REEs in the next decade facing a mined and refined supply that is highly concentrated in China, global and local supply chains will need to navigate significant geopolitical developments, such as China’s recent export restrictions on specific medium and heavy REEs1 and unique sustainability challenges. In addition, the recent rise of REEs to the top of resilience agendas in many countries is expected to accelerate these trends, creating new opportunities for circular REE magnet value chains by resolving current recovery challenges.
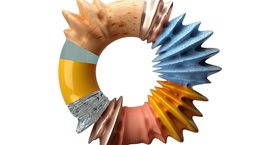
Materials Circularity
This series by McKinsey is a practical resource for leaders looking to build circular value chains.
This article is part of a series on increasing the circularity of materials. To tap into the growing secondary REE market, recyclers can manage volatile scrap pools by evaluating opportunities in appliances and electronics recycling. Doing so will likely require developing and scaling cost-effective technologies for dismantling magnets over the medium term while positioning to capture the uptick in battery electric vehicle (BEV) and wind turbine recycling over the long term.
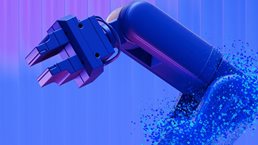
Apple and McKinsey unlock low-carbon sourcing
How recycled materials drive greener supply chains
Demand for REEs is poised to triple over the next decade, spurred by the energy transition
REEs comprise 17 elements, four of which are most commonly used in REE magnets: neodymium (Nd), praseodymium (Pr), dysprosium (Dy), and terbium (Tb). The first two are primary constituents, and the latter two are additives to enhance performance in more demanding applications.
Today, magnetic REEs make up around 30 percent of overall REE volume, but they capture more than 80 percent of the value. Moving forward, global demand for magnetic REEs is expected to triple from 59 kilotons (kt) in 2022 to 176 kt in 2035, driven by strong growth in electric vehicle (EV) adoption, which is outpacing the substitution of REEs with copper coil magnets, as well as the high rate of renewable capacity expansions in wind.
In the absence of production forecasts for China, where most mined and refined materials come from today and where quotas govern mining activities, the currently announced project pipeline could fall short of demand requirements by 60 kt, or roughly 30 percent of total estimated demand in 2035.
In a scenario in which Chinese volumes fill the supply gap until 2035, geopolitical considerations could put additional strain on an industry that has already been plagued by challenges around scaling in other regions, despite increased efforts to build local supply chains.
Local primary supply chains could be insufficient to meet domestic demand
With REE magnets taking on the role of key components in many high-tech applications, overall REE demand is and will likely remain broadly distributed across geographies. At the same time, primary REE production is among the most geographically concentrated materials supply chains, with China contributing more than 60 percent of mined supply and more than 80 percent of refined supply in 2023.1 Zooming in on the trajectory for light versus heavy REEs paints a more nuanced picture. China’s share in light-REE mining and refining could remain at current levels until 2035—despite announcements from other regions—if capacities are added at historical rates. By contrast, current projections show that more than 60 percent of heavy REEs,2 which are key to high-performance uses in wind turbines, EVs, or robotics, could be mined in Asia–Pacific and processed in China until 2035.
Recent geopolitical developments and their effect on trade have renewed ambitions to establish local REE value chains across major geographies, including discussions around how regulatory frameworks can help accelerate development from mineral exploration to magnet production. Although such efforts could lead to a gradual diversification of supply (by reducing China’s share in mining to less than 50 percent, for example), current pipelines and trajectories are likely to fall short over the next five to ten years. In addition, China’s recent export restrictions on specific medium and heavy REEs3 exemplifies risk exposure to additional supply chain curtailments.
Moving forward, secondary supply could become an important gateway to create additional local supply. This is particularly the case when considering notoriously long lead times for opening new mines, environmental concerns, and technological challenges for new entrants to scale and achieve competitive cost levels for REE separation.
Although postconsumer scrap could create significant additional REE supply, recovery remains a challenge
Magnet production could consume an estimated 176 kt of REEs in 2035. Meanwhile, the REE value chain is expected to generate about 40 kt of preconsumer scrap, originating from magnet design and manufacturing steps, as well as 41 kt in postconsumer scrap from various end uses reaching end of life.
In light of environmental issues during mining and processing as well as operational challenges to get primary capacities online, secondary REEs could be an option to increase sustainable sources of supply.
With the majority of downstream magnet manufacturing occurring in China, most REE preconsumer scrap will be generated, processed, and recovered in the region as well, with recovery rates reaching technical limits. By contrast, scrap from postconsumer sources will likely be geographically diverse, although true supply could remain limited to only a few kilotons because of recovery challenges related to already-collected magnets.
Scrap pools are expected to continuously shift from small magnets in consumer electronics and appliances to larger magnets in EVs and wind turbines
Increased use of magnetic REEs for EVs and wind turbines could cause scrap pools to continuously shift by 2050. Today, more than 80 percent of REE scrap originates from applications in consumer electronics, appliances, or internal combustion engine vehicles, all of which use relatively small magnets for motors, actuators, and sensors, among other things.
Although these applications will likely remain relevant over the next ten years, scrap from BEV drivetrains, industrial motors, and wind turbines could reach a similar magnitude, providing a new pool of larger magnets containing higher shares of valuable heavy REEs.
Postconsumer REE recycling could remain challenging, even if more materials were collected
The secondary REE recycling value chain faces constraints for both collection of postconsumer material and recovery of REE magnets. Given that most end uses for REE magnets in the next ten years will be in applications with notoriously low collection rates, such as electrical and electronic equipment from consumer appliances and electronics, there is significant potential to improve collection.
Even if REE magnet collection is improved, materials will likely not be recovered across most applications, especially those with small or medium-sized magnets. Doing so would require dedicated separation of the magnet for further processing, which is a practice currently not adopted within existing recycling value chains focused on high-value or high-volume materials (such as gold and copper or aluminum and steel).
The cost of manual magnet isolation could be prohibitive for the recovery of smaller, lower-value REE magnets
REE magnets are a challenge for today’s recycling ecosystems; devices are partially dismantled, shredded, and then sorted based on their magnetic properties, among other things. As a result, REE magnets may end up in an iron smelter, where they would be lost as slag.
With the total value of REE magnets decreasing as their applications move to appliances and consumer electronics, there is limited room for manually processing components to extract the magnets simply because the cost of the dismantling them would be prohibitive.
Tapping into secondary REE sources today requires addressing new solutions for magnet isolation
Enabling better recovery of REEs will likely require new approaches. On this point, some industry and research organizations are exploring targeted separation (through automated robotic disassembly), bulk magnet isolation (through hydrometallurgy and pyrometallurgy), and hydrogen-based processing (through hydrogen decrepitation). Others are investigating alternative circularity methods—for example, extracting REEs from mine tailings,1 coal-combustion residues, or other residues, such as red mud.
Many of these technologies are still at R&D or pilot stages and need to be significantly scaled before they can be proven at the industrial level. Tapping into the mostly unaddressed pool of postconsumer scrap will likely require players to think through how REE recycling can be integrated into current recycling ecosystems. Two points could help facilitate this integration: First, players that are already extracting other materials from consumer goods can demonstrate what works. Second, multiple materials could be addressed at once by including new steps into established processes or rethinking process chains.
Accelerating the energy transition requires a stable supply of REEs to meet demand for new, more materials-intensive technologies while reducing materials emissions. Recycling postconsumer REE magnets could serve both purposes, and long-term collaborations across the value chain can help address some of the challenges of REE recycling. For example, producers and OEMs can help recyclers focus on the right devices by providing transparency on magnet location, composition, and value—an effort that regulators have also acknowledged is important. Powering the energy transition’s motor begins with understanding the dynamics around scrap pools, which technologies are competitive today and which will be competitive in the years to come, and how to build alliances and integrated value chains to help those technologies get off the ground.