Climate change is creating many life-threatening disruptions, including extreme weather, rising sea levels, and droughts. Faced with irrefutable evidence of global warming, almost 200 countries have committed to the 2016 Paris Agreement, a treaty that calls for accelerated decarbonization. This agreement is designed to limit the mean rise in temperature to 1.5 degrees Celsius from preindustrial levels to mitigate or prevent some of the most dangerous effects of climate change.
While some semiconductor companies have created ambitious targets for reducing their emissions and remaining on a 1.5°C pathway, many others have been less ambitious. The pressure to act may soon increase, however, since businesses across industries are now scrutinizing emissions along their entire supply chain—and in many cases, semiconductor companies will account for a substantial amount of them. Already, some of the semiconductor industry’s most important end customers, including Apple, Google, and Microsoft, have committed to reaching net-zero emissions for their full value chain and set aggressive timelines for achieving their goals.
Some semiconductor companies have responded by setting their own emissions goals. For instance, Infineon plans to reduce greenhouse-gas (GHG) emissions by 70 percent by 2025, compared with its 2019 baseline, and aspires to reach carbon neutrality for emissions directly under its control by the end of 2030. Intel recently committed to net-zero GHG emissions in its global operations by 2040 and has targeted achieving 100 percent use of renewable electricity as an interim milestone in 2030. Several semiconductor players have also committed to science-based targets, including STMicroelectronics, NXP, and UMC. Over the next few months or years, more semiconductor companies are expected to commit to ambitious and actionable emissions targets.
Achieving substantial emission reductions will require collaboration with peers and suppliers, as well as new technologies, innovative thinking, and the complete engagement of fabs. To help companies move forward, we reviewed the current state of greenhouse-gas emissions within the semiconductor sector and collected best practices for abatement. Our analysis allowed us to identify both short- and long-term solutions along the entire semiconductor value chain. This article focuses on scope 1 and 2 emissions, which are the ones that semiconductor fabs can directly control.
Major sources of emissions from fabs
With about 80 percent of semiconductor manufacturing emissions falling into either scope 1 or scope 2 categories, fabs control a large portion of their GHG profile (Exhibit 1).1 Scope 2 emissions, which represent the highest proportion of GHG from semiconductor companies, are linked to the energy required to run their extensive production facilities. The sources of these emissions include the following:
- tool fleets containing hundreds of manufacturing tools, such as lithography equipment, ion implanters, and high-temperature furnaces
- large clean rooms requiring climate and humidity control with overpressure and particle filtration
- extensive subfab facilities for gas abatement, exhaust pumps, water chillers, and water purification
As the node size of chips continues to shrink, energy requirements at production facilities are expected to rise significantly.
Scope 1 emissions, which also significantly add to fabs’ GHG emission profile, arise from process gases used during wafer etching, chamber cleaning, and other tasks. These gases, which include PFCs, HFCs, NF3, and N20, have high global-warming potential (GWP); they rise as node size shrinks.2 Scope 1 emissions may also arise from high-GWP heat transfer fluids that may leak into the atmosphere when fabs use them in chillers to control wafer temperature during manufacturing processes.
Would you like to learn more about our Semiconductor Practice?
Additional emissions may come from upstream scope 3 sources, such as suppliers, chemicals and raw materials, or from transportation to customer facilities. These upstream emissions generally account for only about 20 percent of fabs’ GHG profile, however.
Semiconductor companies also generate downstream scope 3 emissions, which are related to use of products containing semiconductors. These vary significantly by use case. For instance, handheld devices with low power consumption during intermittent usage will have much lower emissions than data centers that operate 24/7. As will be discussed in a later article, product design influences scope 3 emissions, giving fabs little control over them during operations.
Critical levers for emissions improvement
To help fabs achieve substantial emissions reductions and accelerate decarbonization, we identified three areas that need immediate attention, as well as relevant improvement levers.
Decreasing energy consumption
Levers for reducing energy consumption are often directly aligned with other operational targets, such as cost reduction, making them easier to achieve. The many options available can be grouped into two major categories. The first group focuses on reducing tool-related energy consumption—for instance, by upgrading and replacing tools with more energy-efficient ones, implementing smart control systems to enable coupling and regulation of facilities and tools. The second group encompasses activities that involve reducing facility-related energy consumption though various measures, such as exclusive sourcing and use of energy from renewable sources, greater energy efficiency of buildings, and replacing existing lighting in fabs with LED fixtures.
To identify the greatest opportunities for decreasing energy consumption, fabs could look at benchmark-based targets and sources of energy loss. They could also review existing levers for energy reduction by tool and facility type. For instance, fabs might discover that they can improve energy consumption in clean rooms by reducing air pressure, increasing humidity, limiting air exchange in unused areas, or eliminating leaks in air-supply lines.
When optimizing process recipes, equipment engineers typically focus on overall equipment effectiveness (OEE) and give little attention to tool-fleet energy consumption. New incentives, such as rewards for creating energy-efficient recipes, might help change this mindset. Fabs can also help decrease GHG emissions during operation by encouraging experts to share their knowledge of and experience with energy efficiency, using the same tools and mechanisms they employ when sharing strategies for optimizing OEE. To boost their odds of succeeding, fabs can include additional stakeholders in their power-consumption efforts, focusing on external tool suppliers that might be able to modify their equipment to increase efficiency, or those that offer retrofits or energy-saving options for new tools.
Optimizing energy supply
To ensure that sufficient power is always available, fabs often source their electricity from a combination of on-grid and off-grid sources. Most off-grid power comes from fab-owned fossil fuel power plants. Over the short term, fabs can significantly reduce the energy consumption of these plants by pursuing efficiency improvements or switching to alternative fuels such as biogas or green hydrogen. They can generate further gains by developing new off-grid power sources that rely on green technologies, such as photovoltaics, fuel cells, and battery energy storage systems. But these supplies often only complement, rather than replace, a fab’s long-standing on-grid sources.
For on-grid power, fabs may be able to reduce consumption by purchasing renewable electricity from utilities through green premium energy offerings, although the offerings vary widely by region. In Europe and the United States, for instance, renewable on-grid sourcing is readily available and accounts for up to 31 percent of grid energy; in many parts of Asia, however, renewable on-grid sourcing can be challenging because of limited availability (Exhibit 2).
Access to renewable energy may be a major factor as companies decide where they should build new fabs—something that is becoming more common as they try to increase capacity to alleviate the chip shortage.
Reducing process-gas emissions
Process gases can significantly increase global warming (Exhibit 3). Their emissions will vary based on a fab’s age and the sophistication of its abatement technology, but all facilities face some common challenges. Four levers, which are at different stages of maturity, may help reduce process-gas related emissions. Because of economic constraints and other issues, some fabs may not be able to apply some of these levers widely until the technology improves.
Process improvements. Fabs can reduce emissions by adjusting process parameters, such as temperature and chamber pressure. Process engineers often overlook this lever and instead focus solely on yield during optimization efforts, partly because they lack the knowledge and operational experience required to identify strategies for reducing GHG emissions. Similarly, the suppliers involved in daily tool operations and maintenance may prioritize cost and uptime targets over energy savings. If fabs address knowledge gaps and collaborate more closely with tool suppliers, they may improve emissions—for instance, by simultaneously optimizing yield and energy consumption during cleaning protocols.
Use of alternative chemistries. Fabs can sometimes lower emissions by switching to chemicals that have a lower environmental impact. However, they often encounter obstacles when attempting to use these chemistries; for example, it can be difficult to get suppliers on board with their plans. In addition, developing new solutions is both costly and time consuming, as is the process for qualifying new chemicals on existing processes and tools.
To address these roadblocks, fabs could emphasize that GHG reduction is a top priority when communicating with suppliers and note that they want to explore new solutions, including green-chemistry approaches. Fabs could then work closely with their partners to develop a path forward. For instance, fabs and suppliers could jointly create road maps for process-gas substitutions or codevelop alternatives. But even with this push, fabs must temper their short-term expectations about GHG improvement because few green solutions are now viable alternatives to current gases. (While fabs have already implemented some major improvements, such as increased use of NF3, many other shifts, including the replacement of NF3 with F2 or ozone, are still nascent.) Over the long term, fabs could see more gains if they continue encouraging suppliers to explore new solutions.
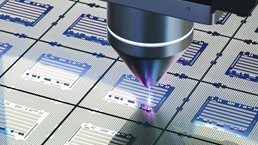
Strategies to lead in the semiconductor world
Gas abatement. Gas abatement will be the main lever to address emissions from process gases over the short to midterm, and this will remain the case until alternative gases with fewer emissions are available, or until gas recycling is widely adopted. Fabs that want to increase gas abatement can select from multiple options, including point-of-use (POU) systems for individual production tools, point-of-area (POA) systems, and central abatement systems. As they roll out and install new systems, fabs must balance the trade-offs related to cost, impact on operations, destruction and removal efficiency (DRE), and timing. Further adoption will also require suppliers to provide innovative technical solutions to do the following:
- Address space constraints, especially in older, 200-millimeter fabs with limited subfab space (for instance, by providing integrated solutions with a smaller footprint).
- Keep by-products, such as nitrogen oxides and carbon monoxide, low while increasing DRE.
- Prevent downtime of production tools during installation and maintenance of abatement systems.
- Enable regular system qualification, without affecting production, to achieve and report higher DREs.
Gas recycling. Fabs can capture unutilized process gases and by-products through various means, such as membrane separation, cryogenic recovery, adsorption, and desorption. They can then refine them into pure process gases that can be used again, potentially reducing process-gas emissions. For this lever to become economically viable, researchers will need to address major challenges related to the separation of process-gas outflows and purification.
Putting GHG emission reduction on the agenda
To help the semiconductor industry meet the critical challenge of reducing GHG emissions, fabs can take four steps to accelerate their decarbonization efforts:
- Create transparency about their scope 1, 2, and 3 (upstream) emissions.
- Set near-term and long-term emission targets.
- Consolidate existing ideas and estimate their expected costs and impact. This will involve defining a portfolio of innovative technologies to be developed jointly with external partners over the next few years.
- Generate an abatement cost curve to serve as a road map for short-, mid-, and long-term decarbonization efforts.
The abatement cost curve can help fabs identify all potential areas for GHG reduction, as well as associated implementation costs and savings. Fabs should first implement the levers that would result in a net cost reduction, and then move to those with net abatement costs that are close to zero and those that will be costly until regulations change or other advances make implementation less expensive. Exhibit 4 shows an example abatement cost curve for a typical fab.
As they embark on their net-zero programs, semiconductor companies will benefit from internal collaboration among staff from R&D, operations, supply chain, and other functions. Among other advantages, such efforts will help ensure that they implement key elements of the decarbonization program simultaneously. External engagement is also essential, since no single company can reach its GHG goals without partners, such as industry peers, suppliers, and customers.
Successfully reducing emissions to remain on the 1.5°C pathway will require both commitment and endurance. While short-term goals are important, semiconductor companies ultimately want to reduce their emissions by about 50 percent within ten years. Within fab operations, many processes or tools may need to be replaced by greener alternatives, some of which are still in the early stages of development. With global warming reaching a critical point, fabs should accelerate their current decarbonization plans and consider developing other green initiatives.