Aluminum is a major building block of traditional industries, such as construction and packaging, as well as the net-zero transition.1 Aluminum is essential for low-carbon applications, such as electric vehicles (EVs), renewable-energy technologies, solar photovoltaics (PV), wind turbines, and related electricity transmission. That said, the production of primary aluminum2 is energy-intensive and can result in significant CO2 emissions when using fossil fuel–based electricity. Furthermore, emissions from the consumption of carbon anodes during electrolysis are particularly difficult to abate, and upstream production and refining processes for primary aluminum (which require the use of coal, heavy fuel oil, or natural gas) can lead to significant embedded emissions.3
Although addressing the consumption of fossil fuels in the production of primary aluminum remains important, recycling aluminum, especially from postconsumer scrap, could be a more efficient and faster gateway to achieving net-zero emissions because it requires only 5 percent of the energy needed for primary production. Momentum for secondary aluminum is building. On the demand side, major customers in the automotive and packaging industries are setting high recycled-content targets for materials, including aluminum. And on the supply side, regulations such as the Critical Raw Materials Act in the European Union and the Inflation Reduction Act in the United States are promoting the development of secondary-aluminum capacity through improved recycling targets and investments in secondary-materials capacity.
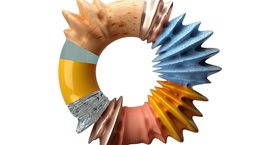
Materials Circularity
This series by McKinsey is a practical resource for leaders looking to build circular value chains.
This article is part of a series on increasing the circularity of materials. To tap the growing secondary-aluminum market, recyclers and customers aiming for circular, lower-carbon aluminum can tackle collection and sortation bottlenecks in the aluminum value chain to boost recycling rates and step up the recovery and preservation of high-value alloys.
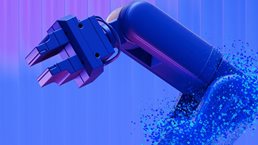
Apple and McKinsey unlock low-carbon sourcing
How recycled materials drive greener supply chains
Aluminum demand is expected to grow by more than 2 percent per annum in the next decade
From 2025 to 2035, global demand for aluminum is expected to increase from approximately 106 to 130 million metric tons (Mt), with demand mainly resulting from growth in energy transition applications and traditional end-use segments, with a CAGR of 2.1 percent per annum.
This increase in demand will mainly stem from growth in the automotive industry and the aforementioned energy applications (an increase of 15 Mt) as well as increased adoption of EVs, which typically have higher aluminum content than internal combustion engine vehicles.
The majority of growth on the supply side could come from secondary aluminum, mainly driven by greater availability of postconsumer-scrap volumes in China. At the same time, primary production will likely account for about 30 percent of supply growth, based on the committed project pipeline.
Optimizing circular aluminum value chains could bolster supply
The following feedstocks of secondary materials can help support increased demand:
- Preconsumer scrap. Aluminum scrap coming from casting, semiproduction, and fabrication accounts for approximately one-third of the global scrap pool.1 These volumes typically have high rates of collection and can be directly remelted.
- Postconsumer scrap. Aluminum scrap coming from end-of-life applications accounts for the remaining two-thirds of global scrap.2 Postconsumer scrap requires adequate collection as well as further steps for sortation and shredding before it can be refined and melted for reuse.
The high share of mixed scrap is a key challenge for aluminum recycling
In manufacturing processes and products, aluminum is often commingled, making it difficult to recover and preserve specific alloys. In many cases, this can limit recycling of mixed scrap and cast alloys.
Preconsumer scrap accounts for about one-third of total scrap volume, while the remaining volumes come from postconsumer scrap. With current industry practices, a large share of postconsumer scrap is not segregated and ends up in mixed-scrap pools, where it is eventually downcycled, without specific high-value alloys being recovered. For example, 6xxx-series alloys (classified by their magnesium and silicon content) see lower rates of recycling and are mostly used in 7xxx-series or cast alloys, which can handle a higher share of impurities.
With the growing share of EVs, mixed scrap traditionally used in cast alloys for internal combustion engine blocks could see its demand reduced along with the decline of automotive castings, resulting in a need to improve sortation and recycling practices.
Although aluminum is already highly recycled today, there are large discrepancies between regions and grades of alloy
Collection and recovery rates of aluminum scrap vary across regions and scrap sources.
Preconsumer scrap has high rates of collection and recovery, primarily because of its high value and the relatively limited diversity in the scrap flow.
By contrast, postconsumer scrap has comparatively larger collection and recovery losses, although differences exist across end-use segments and regions. For example, collection rates in beverage packaging vary significantly from country to country, ranging from 75 percent in the broader European Union to 99 percent in Germany.1 For other types of packaging, such as aluminum foil, collection is low and difficult to implement, and material can often get lost in municipal waste.
In addition to tackling the challenges of mixed-scrap pools, improving collection and recovery rates could lead to additional opportunities to improve overall recycling rates
In specific regions, such as China and North America, there is potential to increase collection rates. For 5xxx-series alloys, which are mainly used in transportation and building structures, approximately 6.2 Mt of aluminum could remain uncollected by 2035.
Regulations and improved infrastructure could increase usable scrap pools and subsequently improve collections rates. Doing so would likely entail separate municipal and industrial waste collection schemes, which could reduce the share of aluminum scrap that is collected but unrecovered.
Recovering specific alloys from mixed scrap requires improved sorting practices
Today, most mixed scrap is either exported for manual sorting in best-cost locations or downcycled without specific, high-value alloys being recovered. Advanced sortation and repurification can help address this challenge.
Of the two, advanced sortation is already cost-competitive, but it requires significant work and commitment to launch at scale. An exemplary advanced-sorting process entails producing twitch (a key raw material) from Zorba1 through a combination of technologies—X-ray fluorescence, X-ray transmission (XRT), and laser-induced breakdown spectroscopy—that separate light and heavy fractions. From there, aluminum scrap could be sorted into cast alloys and individual wrought alloys (such as 5xxx or 6xxx), reducing the share of downcycled aluminum. With today’s technologies, a scale of 30,000 to 40,000 metric tons of scrap per annum could allow processing costs of about $200 to $300 per metric ton2 and create a positive business case with a margin of $50 to $150 per metric ton—with higher-value metal fractions offsetting the additional processing efforts.
By contrast, repurification technologies could help produce 1xxx-series alloys. However, repurification and other technologies typically consume more energy and are at earlier stages of development than other technologies.
Although advanced sorting technology has progressed significantly over the past few years, setting up such circular value chains remains challenging, and there is significant potential for greater efficiency. Moving forward, tackling mixed scrap could benefit from collaborative approaches to align stakeholders across local value chains. Such alliances can help pool resources, share knowledge, and invest in advanced technologies, which could therefore streamline operations, accelerate learning curves (subsequently reducing costs), and improve the overall efficiency of the recycling process. Through back-to-back offtake agreements and synergetic commercial models, alliances could also help ensure that partners commit over the long term, which is particularly important when securing a continuous flow of scrap materials.
A number of recent alliances demonstrate the potential of partnerships to tackle these challenges. For example, Constellium’s collaboration with OSR is working on enhancements to LIBS with the longer-term goal of extracting high-value aluminum from end-of-life vehicles,3 while Hydro’s advanced-sorting partnership with Padnos enables more upcycling of postconsumer scrap.4
Such collaborations benefit all parties involved—for example, scrap collectors can gain access to better sorting technologies, recyclers can secure a steady supply of scrap, and end users can meet sustainability goals while reducing their carbon footprints through offtake volumes.
Collaborations across the secondary-aluminum value chain can help address some of the challenges of aluminum recycling and increase rates of production. Therefore, an ecosystem-wide approach involving scrap collectors and aggregators, providers of advanced-sortation technology, remelters, and end user offtakers is critical to establishing cost-effective generation of higher-quality scrap and products with high recycled content while avoiding downcycling.